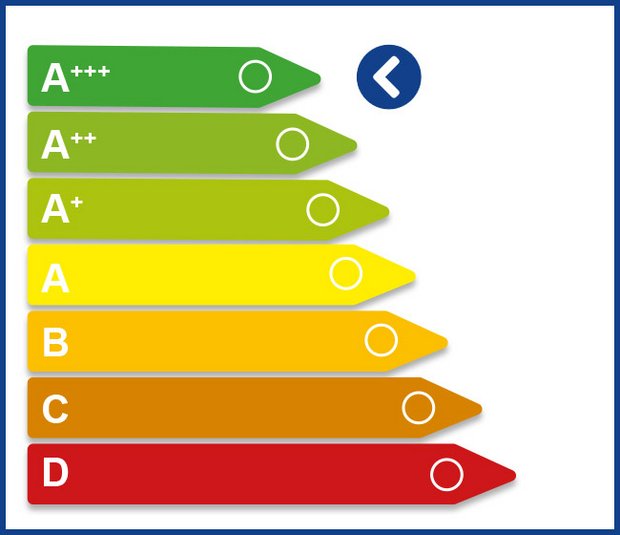
LASER WOBBLE WELDING ECOLENER SERIES:
Energy Class A+++
Energy saving has become a priority for welding industry. This is due to the recent increase in energy demand and constraints in carbon emissions. Increasing environmental demands from governmental and customers strain the importance of reducing the environmental pollution while welding. Therefore, the minimum energy-oriented green welding process is must. Wobble Laser Welding (WLW) is considered to be the most significant development in metal joining and is a “green” technology due to its energy efficiency, environment friendliness, increased speed, reduced postprocessing and cleaning, and versatility. As compared to the conventional welding methods, WLW consumes considerably less energy. Our Wobble PRO+ EcolEner Series are the most enrgy saving laser Welding machines on th emarket with a wall-plug efficiency of almost 50%. Compared no normal Laser Welding machines is this a almost a 20% more energy saving!
Go to Ecologic Green Welding with Wobble6-PRO+
NEW and MUCH Greener: Wobble6-PRO-Plus-ECO
Wobble6-PRO+ECO: Our BEST and most Ecological Handheld Laser Welding Machine with full welding control in the Torch
NEW: Wobble6-PRO+ECO
Wobble Laser Welding is SO MUCH Better!
Although the laser was only invented in 1960, it quickly became established as a production process and by the 1980s was starting to be used in high volume manufacturing. Recent advances which have improved the beam quality and efficiency of lasers, make the laser an even more advantageous solution to high volume or automated industrial joining.
Weld quality and consistency
Laser welding enables the quality and consistency of welding to be readily controlled and consistently maintained. Since the laser head makes no contact with the workpiece and there is no electrode which can become worn, eroded or damaged there is no need for a tool change where the electrode needs to be reground or sharpened, as is the case with TIG. The lack of electrode dressing in laser welding results in higher uptime and longer time between maintenance interventions. Also, there is no risk of contamination of the weld material with Tungsten from the TIG electrode tip when striking the arc.
Lower heat input
With laser welding the heat input to the metal being welded is lower which means there is a smaller heat affected zone (HAZ) and the distortion of the assembly is vastly reduced making complex and accurate assembly more achievable, especially in an automated setting. In addition, the lower heat input means that a weld can be placed close to sensitive electronics or other heat-sensitive materials without risk of damage or failure. An example of this is in cardiac pacemakers and defibrillators where the external weld seam is directly above a heat-sensitive battery and micro-electronics which cannot withstand a temperature over 80 degrees C.
Throughput – higher welding speed
Weld speeds are generally higher with laser welding, especially with modern high power continuous wave (CW) fibre lasers. A high welding speed sometimes means that the motion system, for example the CNC system, robot contouring speed or human arm, is the limiting factor on cycle time rather than the process.
Cost per metre of weld
In processes where throughput is high it is common to find that the laser solution is more efficient and results in a lower cost per metre of weld. Interestingly, there are processes which our wobble welding achieves deeper penetration and higher welding speeds. This Wobble process typically use a combination of laser welding to heat the metal efficiently to melting point and rotation of the welding beam to provide deposition of droplets into the weld pool and enhanced penetration and weld strength over either process as a stand-alone procedure.
No finishing of the weld
With the inert gas shielding, a laser weld in stainless steel or aluminium normally requires no post-processing (grinding or dressing) after welding, the weld finish is bright and oxide free and can be typically coated or painted without further cleaning steps.
Access difficult areas
Since the laser beam is a “line of sight” process, the laser can pass through gaps in a structure to weld areas from the rear, where it would not be possible to introduce a TIG electrode. Using a camera to view through the laser optics of robot or cobot versions, it is easy to align the beam to a precise feature and perform welds in difficult-to-reach parts of the structure.
What about gaps?
One disadvantage of laser welding is that it tends to rely on good contact and minimum gap between parts to be joined, but with the wobble solution, this disadvantage disappeared completely. With our laser Wobble process there is no need anymore to ensure that gaps are minimised or avoided to ensure good results. With in plus the addition of our digital wire feed, which adds a certain complexity to the process, it is possible to fill gaps or build up areas for additional strength.
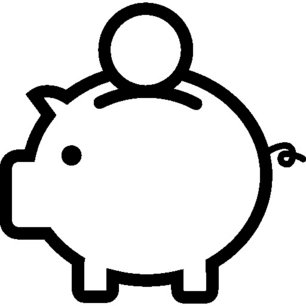
Far More Cost-savings
Respect the enviroment better than any other welding machine
With the small footprint design and its electro-optical conversion efficiency which is higher than 35%, and it's maintenance-free concept,( laser source is designed to resist more than 100.000, hours lifetime) our Wobble laser Welding machine is far more costeffective and far superior to other types of lasers of the same power. We have adopted the international standard optical fiber QBH output head and international standard serial port controls. The chiller is installed with a filter, which is safe and environmentally friendly, 4% more energy-saving and more durable, and stable working performance with longer service time than before.time than before.
Wobble6-PRO+: Standard equipped with our Wobble-Drive2 high precision wire feeder.
WOBBLE-DRIVE2 – precise wire feeding for professional welding seam results
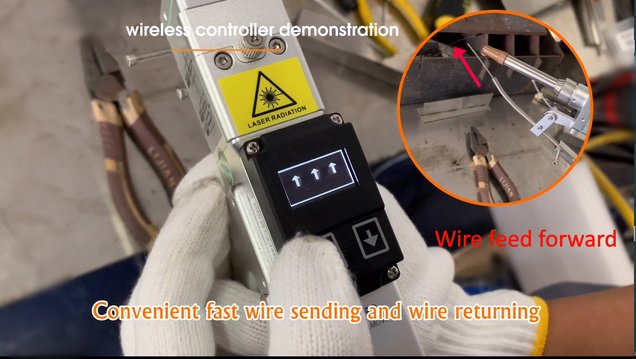
Wire-feed control from welding torch
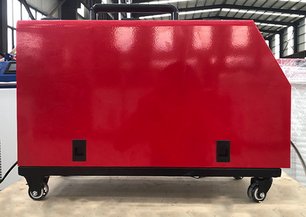
The advantages of the compact and robust WOBBLE-DRIVE2 at a glance:
- Wire speed adjustable from 0.2 to 8.0 m/min
- Fine adjustment of wire speed in steps of 0.02 m/min
- prepared for wires of 0,8 - 1,0 - 1,2 - 1,6mm
- 2 driven wire feeding rolls for minimal slippage and maximum feed constancy
- Fully integrated into welding system Controller
- Full digital motor control - speed - forward - backward - retract
- Individually customizable wire retraction
- Finely adjustable interval function to define the seam shaping and optics
- Standard remote controller (potentiometer or up/down) – for automated laser welding
- Single standard low voltafe connection / quick coupling
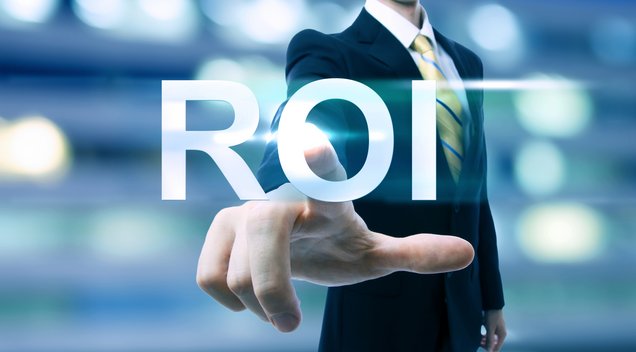
Start Earning GOOD money With our NEW WOBBLE-PRO-Plus Series
Full CE Certified
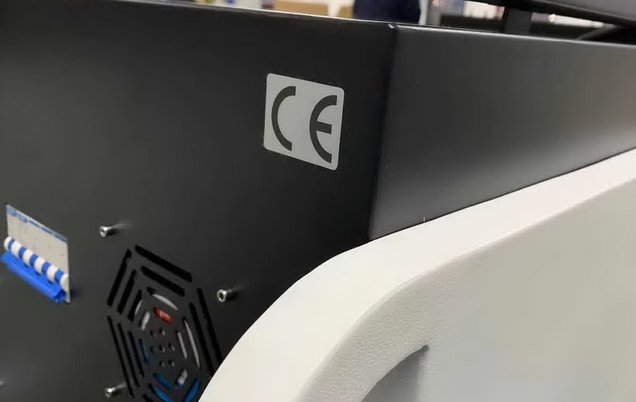