Energy Class of the Welding Processes
See for yourself which one is best!
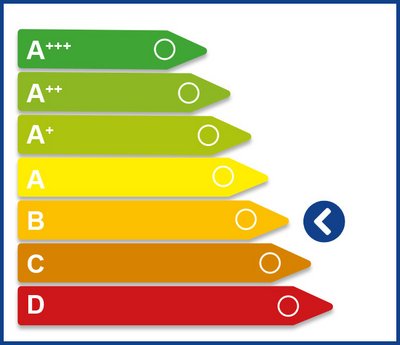
Metal arc welding (TIG/TAG)
Class B
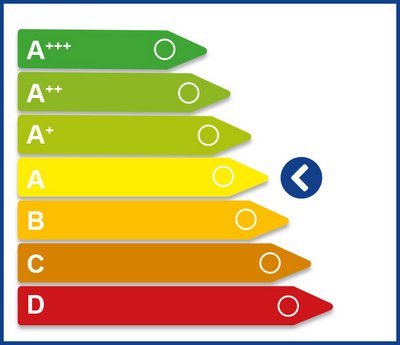
Plasma Beam Welding
Class A
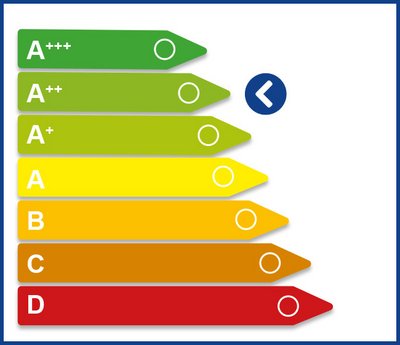
LASER WOBBLE WELDING
Class A++
Les avantages du soudage au laser par rapport au soudage à l'arc
Les concepteurs de produits et les ingénieurs de procédés qui envisagent le soudage au laser comme une alternative aux types de soudage plus conventionnels, tels que le soudage à l'arc MIG/TIG, trouveront que chacun a ses avantages et ses inconvénients. Mais pour de nombreuses applications, le soudage au laser est une méthode de soudage plus propre, plus précise et plus contrôlée, et est surtout beaucoup plus rapide et mieux contrôlable.
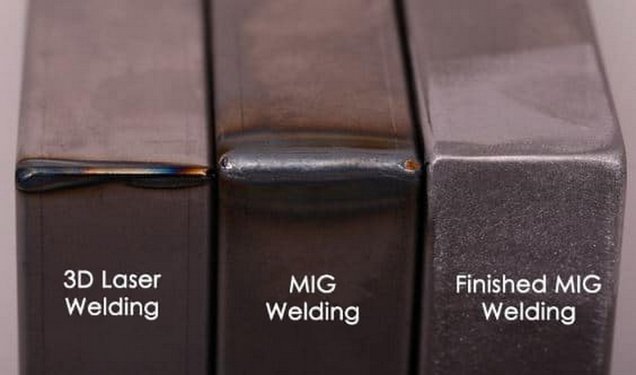
How is laser welding better than TIG?
What are the main benefits from manual laser welding compared to manual TIG welding
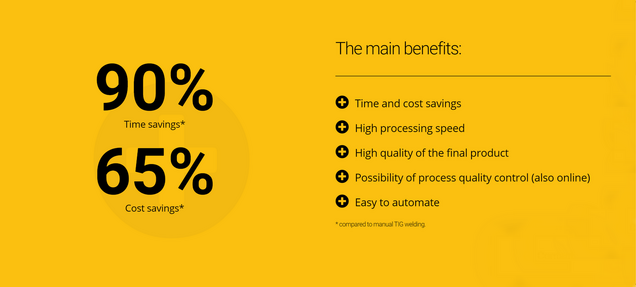
Laser welding Versus Arc Welding
Before comparing the two methods in detail, it’s helpful to review how each of them works:
Laser Welding
In laser welding a laser beam is focused to a point usually just below the surface of the metals to be welded, causing the metals to heat and melt at the point of the weld. In their liquid state the two metals combine so that when they cool they are bonded. The laser beam has a high-power density (typically 10 MW/cm²) producing very small, Heat-Affected Zones or HAZ zones. These are typically fractions of a millimeter to a few millimeters in diameter and they heat and cool very rapidly.
ARC Welding
Say the word “welding” and most people will immediately think of a person holding an acetylene torch like the kind they may have used in high school shop class. Today’s industrial welding, however, is typically arc welding in which the heat source is an electric arc formed between an electrode and the base metals being welded. The two main types of arc welding are TIG and MIG.
In TIG (Tungsten Inert Gas) an inert gas flows around the electrode to protect the weld from contamination. In addition to the electrode the welder also holds a stick of filler (flux) that melts in the heat of the arc and that, when cooled, bonds the metals. Excess filler that solidifies around the weld, called slag, must then be removed, usually by grinding. As filler sticks are con- sumed during welding they are replaced.
MIG (Metal Inert Gas) is similar to TIG except that the electrode itself is composed of the filler material. The electrode is therefore consumed during welding and must be replaced when depleted.
Comparing speed of laser welding versus tig welding
Lasermach PhotonWeld Series - Real portable welding machine - laser welding versus TIG welding
Comparing Laser Welding to MIG and TIG Arc Welding
Types of material to be welded. Lasers can weld many types of materials together including many types of stainless steel, titanium, copper, and aluminum (although the two pieces being welded must be different kinds of aluminum). However, not all metal combinations are “bondable.” In conventional welding the metals don’t bond directly with each other but with the filler. So metal-to-metal compatibility is not an issue — which is why conventional welding can weld more types of metal than laser welding.
Material thickness. Laser welding is suitable for jobs ranging from as thin as 100µm up to about 8 mm (in the case of steel). That means that laser welding can be used for jobs where the metal is so thin that conventional welding would destroy it. On the other hand, conventional welding can easily handle large pieces — such as large pipes or structural beams in a building — that laser welding can’t.
Precision. The power output, size of weld, depth of weld, speed of weld, and the track of the laser beam on the metal surface are all highly controllable. The result is a very precise weld — you heat just what you want to heat to the degree you wish to heat it. Among other advantages versus conventional welding, there’s less likelihood of damaging or deforming the surrounding surfaces or components like electrical components that may already be installed.
Automation. Another benefit of a highly controlled process is that laser welding is highly programmable and robotic. Since it’s easier to automate compared to MIG or TIG welding methods, greater repeatability and faster throughput can be achieved.
Contamination. With laser welding, the only materials involved are the metals to be welded. For best results the metals must be cleaned of any oil and dirt prior to welding. The welding itself introduces no filler or slag that could contaminate application environments, such as an operating room in the case of surgical instruments.
Environmental impact. A cleaner process also means there’s much less impact on the environment.
Corrosion. With some metals such as steel, aluminum and titanium alloys, brittleness can result from conventional welding if the electrode used for welding contains traces of moisture. The heat of the welding causes the water to decompose and release hydrogen that enters the metal causing it to become brittle. This can’t happen with laser welding because there is no electrode.
Left picture : TIG welding with big heat affected zone -- Right picture laser welding with much smaller heat affected zone and much finer welds
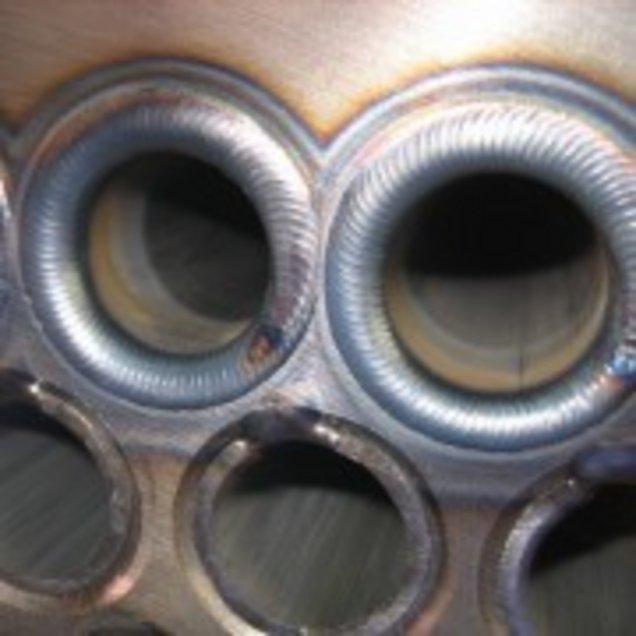
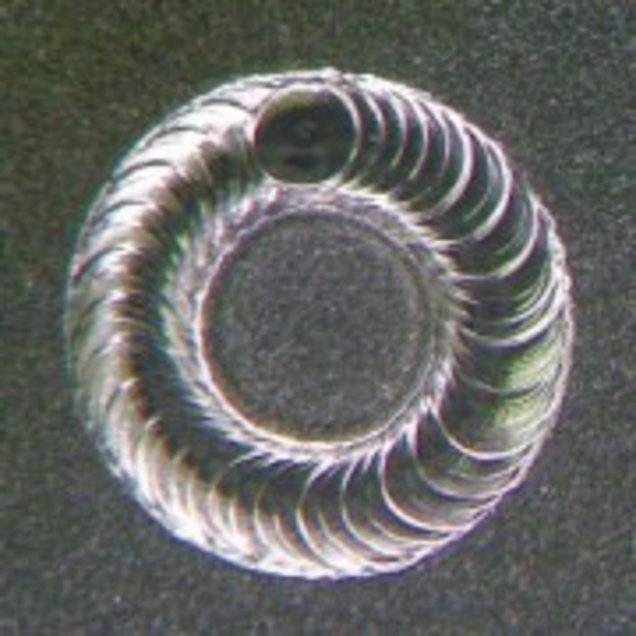
LASER WELDING ADVANTAGES |
- Cleaner — no excess bonding material or slag to clean off |
- Less possibility of contamination |
- Can weld more complex shapes |
- More precise — for smaller objects, tighter spaces |
- Can weld thinner metals |
- More highly repeatable results |
- Easier to automate |
- Less chance of deforming or damaging nearby areas |
- More environmentally friendly |
- Less likely to corrode |
ARC WELDING ADVANTAGES |
- More suitable for welding large structures |
- Wider range of materials can be welded |
- Can weld thicker materials |
The Laser Machining Advantage
The value of laser cutting, welding, marking, drilling, and other laser machining techniques has become increasingly known in the medical industry, causing further evolution of laser machining technologies to serve medical device manufacturing needs. Laser working resolutions/tolerances have improved dramatically, speed has increased.
Following are eight key benefts of laser machining that applies to many different medical industry applications.
1. Precise Temperature Control.
The high-performance materials used today in the industry often have desired material properties that are extremely sensitive to severe temperatures. Many special metals behavior are adversely affected by the temperature profles typical in Tig and Mig welding processes. Fortunately, laser welding of this special metals, and other delicate materials can be performed reliably with minimal heat-affected zones (HAZ) by laser welding. The temperature exposure of a material during laser manufacturing can be controlled in the range of micrometers, including how deeply the beam penetrates a material. The ability to program and precisely control the laser's output power and material exposure time, makes laser cutting a highly reliable and repeatable process.
2. Incredible Geometric Tolerances.
High-Tech device's geometric features are becoming more complex and new applications and techniques are being pioneered. Moreover, these new geometries often require much tighter manufacturing tolerances that are extremely repeatable. Modern laser machining beam widths are extremely small, some laser frequencies are even small enough to provide tolerances in the realm of tens of micrometers. Laser machining controllers are also extremely precise and consistent in the cap X and Y plane, allowing for complex and tightly spaced curves and segmentation during laser welding of fine wires. Automation features available with laser welding tools also enable much smaller tolerances with software-driven operation based on CAD Models. Benefts : technology is advancing rapidly with designers exploring various metal combinations for longer resistance and durability. Combinations like titanium and steel become challenging to weld properly and cleanly with any other method than fiber laser welding.
3. High Repeatability.
The level of automation and software control driving some robotized laser welding processes, as well as the very tight tolerance control, provides a level of repeatability and quality diffcult to achieve with other manufacturing technologies and methods. The precise control of laser power, pulses, and processing temperature further enhances the overall repeatability of laser machining. Laser machining systems also have very high up-times with little need to re-tool processing components, which means there is little variation in the machine itself from part-to-part and batch-tobatch. Laser machine operators familiar with mechanical manufacturing qualifcation requirements may also have expertise in methods to enhance overall repeatability and qualifcation assurance protocols.
4. Faster Processing Speed and Shorter Lead Times.
As many mechanical devices designers may be interested in iteratively improving a design with a short delivery window, or prototyping several design variations simultaneously, cost effective and rapid manufacturing is often a necessity. Traditional precision manufacturing technologies, such as CNC machining, EDM, and
casting sometimes require substantial lead times for fxture, tool, and mold designs. Making modifcations to these processes can also incur large extensions on lead times, as well as huge costs in the case of mold making. The software driven approach to laser machining systems and simplifed setup enables much shorter lead times and faster job processing speeds. Also, the high up-time of laser machining tools means that there is very little lost time, and job-to-job transitions can be performed without long tool cool-downs and warm-ups. As with most manufacturing and mechanical technologies, time is money, and laser welding tools provide competitive advantage for prototyping and production volume manufacturing.
5. Reduced Contamination from Flux, Pigment, and Debris.
Many mechanical device and appliance technologies are required to pass strict safety requirements and quality assurances protocols. Areas where contamination
is a particular concern are with high-tech appliances. Most traditional machining technologies produce a substantial amount of debris, or involve complex chemical processing stages. Flux, pigments, and solvents must thoroughly be removed to meet the stringent quality requirements. In the case of laser machining, many of these steps are unnecessary, as laser welding, and other laser processes don’t require any chemicals, flux, or pigments and the laser machining produces minimal debris.
6. More Durable Weldings.
The rigorous sanitation requirements for many high-tech appliances and tools frequently requires the tools to be placed in extremely harsh sanitization chemicals or under high heat and moisture environments. Most welding technologies, and even early laser welding, had diffculty maintaining welding that doesn’t flake, erode, or develop oxides or corrosion byproducts. The latest laser welding techniques are precise and controlled enough to produce marks that don’t produce debris.
7. Reduced Machining Costs and More Cost Effective Validation.
High-tech devices and appliances requirements often place them in a high cost category for traditional machining. The levels of precision, repeatability, and
purity expected for this complex applications may be far too expensive to be performed by technologies other than laser machining. Modern laser machining
tools require very little maintenance and can readily be automated, reducing the overall cost of operation compared to many machining technologies.
Validation protocols required by quality assurance standards can also often be performed easily with laser machining technologies high controlled processing features, further reducing the manufacturing overhead for laser machining services, respectively.
8. Enables Advanced Materials and Approaches.
The latest mechanical devices are often high-mix parts with a wide range of materials in a single part. Part sealing, mixed material welding, and machining of a wide range of materials is often required to produce a single device. The precise control over the laser beams frequency, power, and pulse enable laser machining technologies to operate on a very wide range of materials. Various and mixed metals and polymers can be laser welded, including clear polymers and the latest in organic bio-absorbable material
CONCLUSION
The best way to compare laser welding to arc welding is on the basis of your own product and production requirements.
- Are you looking for a very precise weld?
- Do you require an intricate weld pattern or is the area to be welded difficult to reach?
- Is minimal cleanup, low contamination risk, and low environmental impact important?
- Do you need to integrate welding with other manufacturing steps — so automation and high repeatability are both key?
If you answered yes to any or all of these questions then you may wish to consider laser-welding, especially if the metals to be welded together are thin. One way to know for sure which method of welding is best is by discussing your application with a laser-welding expert first, before you commit to a process.