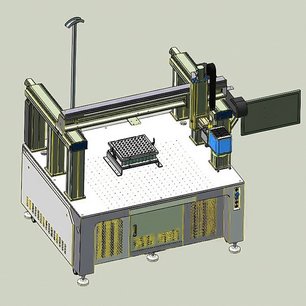
Laser Welding of batteries = High Speed Solution
As the laser Welding process is non contact and the beam is steered by motion of the head, the welding speed is determined by the tab materialsa nd thickness and the terminal material along with the selection of laser power. As an example a 0.4 mm thick nickel plated copper tab can be welded to an aluminum terminal in 10 milli Seconds
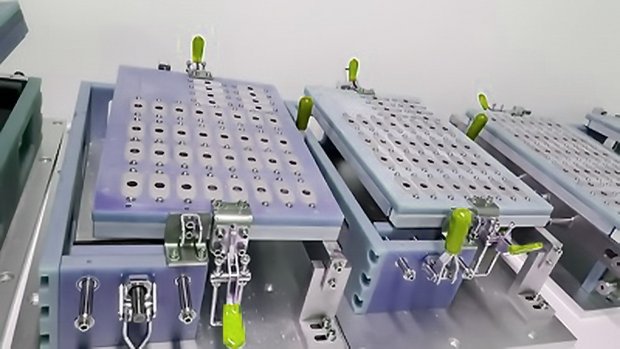
Battery Pack Manufacturing Solutions
When planning an automated or semi automated solution based on our Wobble cube, the primary factors to consider are loading/unloading, motion and tooling that fit the planned production flow and production rate.
Loading and unloading can range from manual to conveyer or pick-and-place, motion options center around whether the laser head or the part will be moved, with options including XYZ tables and gantry’s or robotic manipulators. For tooling, the laser is non contact, so tooling of the parts can be achieved either by using a fixture that the batteries and tabs are loaded into, or using actuated tooling that is deployed prior to the welding process.
The most suitable technology and process for battery pack manufacture relates to a number of factors including the pack size, thickness and material of the tab itself, and the necessary production rate. Laser welding processes enable high quality volume production, and, of the two joining technologies today used, spot welding and laser welding, the selection is usually made based on the specific requirements in each situation, but laser welding is taking over very fast from the spot welding, especially with the excelent wobble laser welding technology.
280A Big LifePO battery cells welding
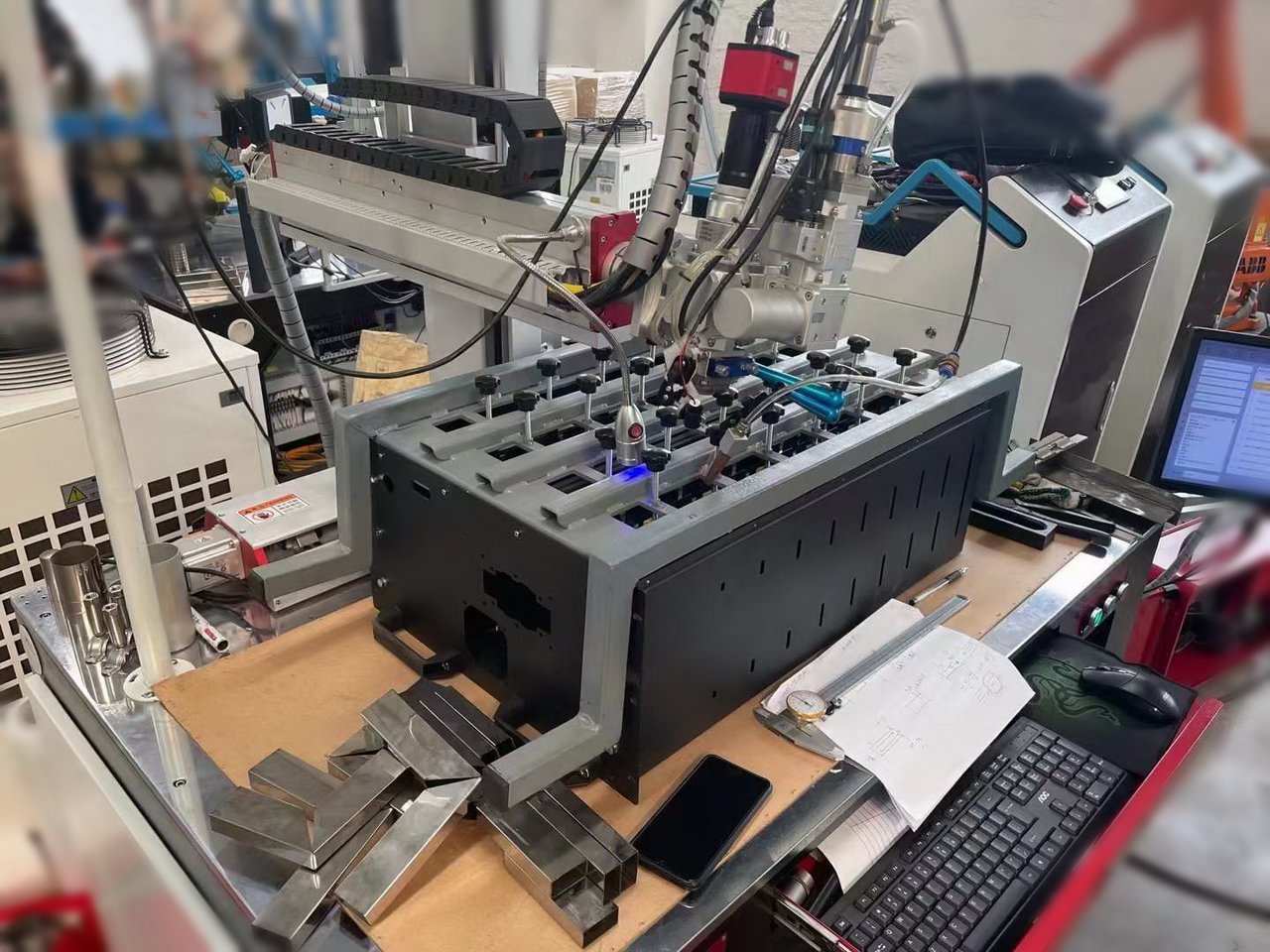
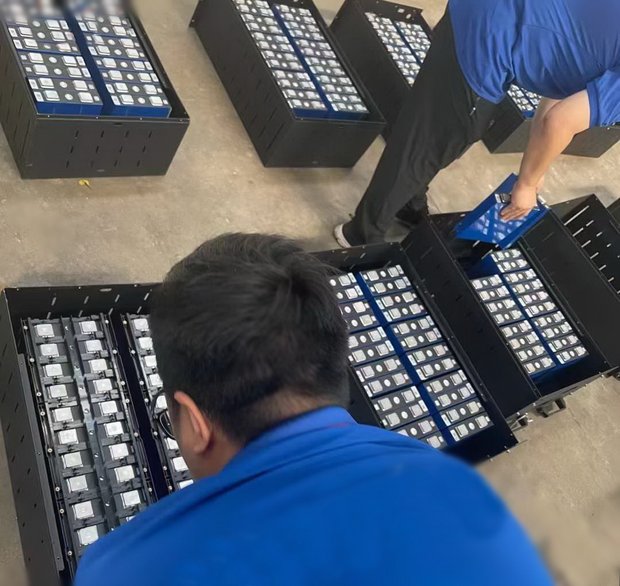
Laser Wobble Welding – Flexible Weld dimensions
As laser welding has no limitation on the proximity of the welds, the laser can place any pattern of weld spots on the tab or with the wobbling technology the wobble laser can weeld any diameter of circle according to strength requirements. If the weld strength of the joint is achieved, conductivity follows.
For more conductive materials, the weld area required for strength can be as much as 10 times that required for conduction. Although peel strength remains an important weld test, vibration is also important. As vibration strength places an emphasis on having good weld strength in any direction, the circle weld of wobble welding provides the solution.
Laser Wobble Welding in Battery Pack assembly
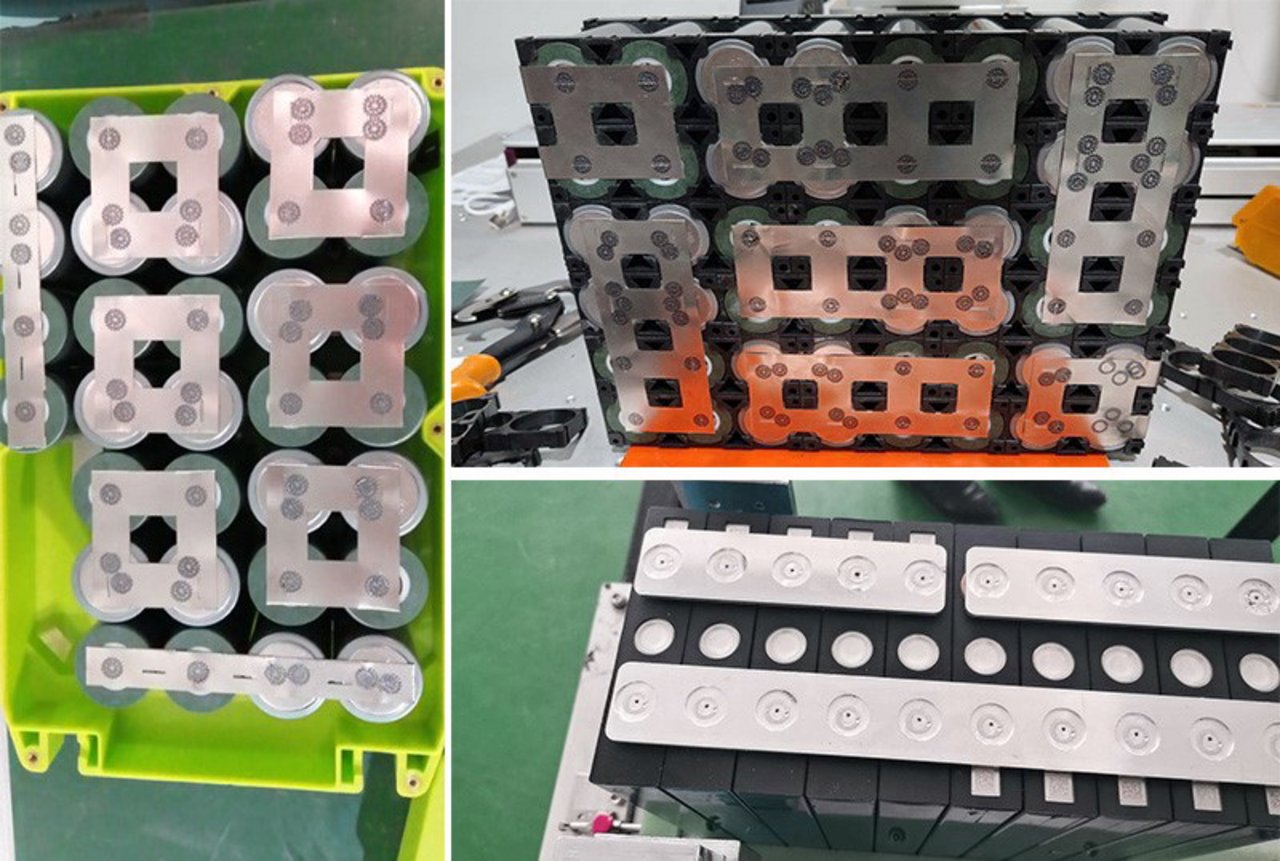