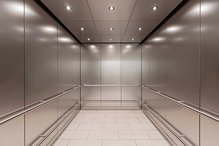
Stainless steel is an exceedingly versatile material.
It is preferred where the properties of steel and corrosion resistance are required in tandem.
Its first use was in cutlery but due to its corrosion resistance properties. Next, it found its way to the chemical industry. Today, we can see stainless steel pretty much everywhere. The use-cases vary from industry to industry.
A few industries that use stainless steel extensively:
- Food and catering
- Chemicals and pharmaceuticals
- Medical equipment manufacturing
- Architecture and construction
- Home appliances
- Offshore and shipbuilding
- Automotive manufacturing
- Energy and industry
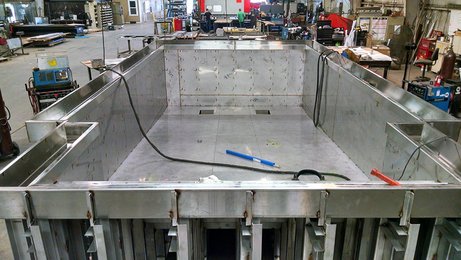
Laser Welding of Stainless Steel
Wobble-3+: Optimal solution for High speed high finish welding of stainless steels
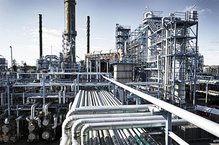
The demand for stainless steel is annually growing at a whopping 5%.
In 2019, global production of Stainless Steel reached over 52 million tons.
At present, a wide number of industries utilise stainless steel. Aside from traditional and marine constructions, household appliances are also experiencing a rise in usage. While stainless steel is more expensive than mild steel, its excellent properties lead to increased service life and reduced cycle cost. So the larger upfront costs pay off in the longer run.
Stainless steel brings along corrosion and heat resistance besides the conventional properties of steel. It provides all the advantages of steel along with a few of its own. It does not corrode easily, endures rough environments better and has a longer service life.
But it is not completely true that it is stain-proof. Firstly, the resistance to corrosion depends on the grade. However, abnormal surrounding conditions such as low-oxygen, poor circulation and high salinity may stain it irreversibly.
Despite the above risks, stainless steel is a wonder material and has a highly positive impact on the industry as a whole. Due to so many grades with different properties, there is always a grade that is perfect for an application. It is essential to choose the grade wisely to ensure a cost-effective investment.
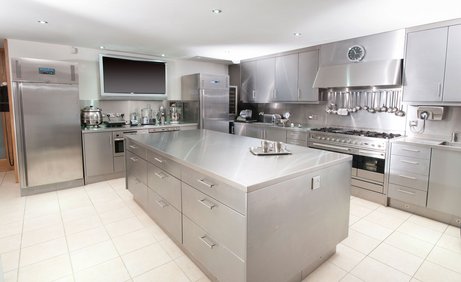
Grades of Stainless Steel
There are hundreds of grades of stainless steel in the market today. Choosing the right one for your application is important as their properties can be quite different from each other.
Types Of Stainless Steel:
There are five types of stainless steel, which are categorized based on their microstructure (microstructure in a key influencing factor in how strong the steel is going to be). Three out of the five steel types are most commonly found in fabrication shops:
- Austenitic stainless steel – the most commonly used material
- Martensitic stainless steel – used for hard facing and other high-wear applications
- Ferritic stainless steel – most commonly used for consumer products as it’s cheap to make
Each kind has it’s own benefits and difficulties when it comes to welding. The technique used to weld stainless steel is not all that different from that required to weld standard carbon steel, with two exceptions. Firstly, you must exercise more care and control with regard to heating and cooling stainless steel, and secondly, it’s more important to properly match filler metals with the material being welded.
The AISI (American Iron and Steel Institute) system for naming stainless steel is still used by the industry. The numbering system uses three-digit numbers starting with 2, 3 or 4.
200 series
This series is used for austenitic grades that contain manganese. These chromium manganese steels have a low nickel content (below 5 per cent).
200 series find use in:
- Washing machines
- Cutlery
- Food & drinks equipment
- Automotive industry
- In-doors equipment, etc.
300 series
This series is used to name austenitic stainless steels with carbon, nickel, and molybdenum as alloying elements. The addition of molybdenum improves corrosion resistance in acidic environments while nickel improves ductility.
AISI 304 and 316 are the most common grades in this series. AISI 304 is also commonly known as 18/8 steel as it contains 18% chromium and 8% nickel.
300 series stainless steel applications include:
- Food & beverage industry
- Automotive industry
- Structural for critical environments
- Medical instruments
- Jewellery, etc.
400 series
Ferritic and martensitic alloys form this series of stainless steel. These grades are available for heat treating. Providing a good combination of strength and high wear resistance. The corrosion-resistance properties are lower than 300 series, though.
Applications for 400 series include:
- Agricultural equipment
- Motor shafts
- Gas turbine parts, etc.
Preparing to Weld:
As in any type of welding, it is very important to clean stainless steel before welding it. What you may not realise, however, is how important it is to only use the tools that you use on stainless steel, on stainless steel. Tools such as brushes should be kept separate for stainless steel projects because of how sensitive the material is to the presence of any carbon steel. The same is true of stainless hammers and clamps, because trace amounts of carbon steel can become embedded in stainless steel causing it to rust.
Similarly, grinding carbon steel in proximity to stainless steel can result in the same problems. Carbon steel dust that is suspended in the air can land on stainless steel and again lead to rusting. So it’s a good idea to keep carbon steel and stainless steel work areas totally separate.
The other important factor in preparing to weld stainless steel is making sure you have the proper filler material, which means you will need to be aware of exactly which type of base material you’re welding. There are, of course, situations where it is not as simple as this, like when you are doing on overlay, or joining dissimilar metals.