Green Welding: eco-friendly, cost-effective
Wobble-PRO Series: Ecological responsable welding
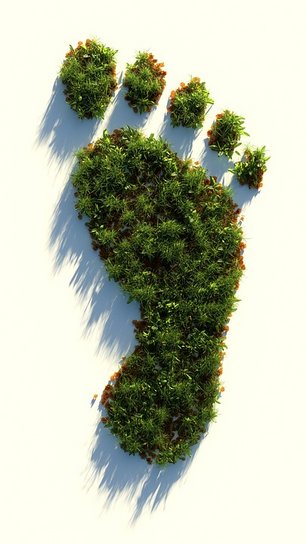
Wobble Welding: eco-friendly, cost-effective, sustainable and real greener
Better welding methods reduces CO2 emissions!
Energy saving has become a priority for welding industry. This is due to the recent increase in energy demand and constraints in carbon emissions. Increasing environmental demands from governmental and customers strain the importance of reducing the environmental pollution while welding. Therefore, the minimum energy-oriented green welding process is must. Wobble Laser Welding (WLW) is considered to be the most significant development in metal joining and is a “green” technology due to its energy efficiency, environment friendliness, increased speed, reduced postprocessing and cleaning, and versatility. As compared to the conventional welding methods, WLW consumes considerably less energy.
ENERGY EFFICIENCY IN WELDING TECHNOLOGY
The global discussions on climate change and the environment are increasingly calling the use of resources and energy consumption in production into question. "Sustainability," "life cycle assessment" and "energy efficiency" are terms used in these discussions that are particularly critical of production and manufacturing processes. Energy efficiency in relation to climate change is one of the most important issues today. Currently, 75% of the energy supply is based on the consumption of non-renewable (nuclear and fossil) energy. Increasing energy shortages as well as climate problems demand a significant reduction in the use of non-sustainable energy sources. An efficient use of energy is therefore absolutely paramount to the preservation of our livelihood. With our Wobble Laser Welding Technology we help to reduce the energy losses.
Joining processes consume significant amounts of energy and resources.
The generation of energy efficiencies is a technologically and economically complex subject area. Not only electrical performance data should be evaluated, but a complete view of the manufacturing process should be considered as well. The energy input, degree of melting, welding speed and cost efficiency should be carefull examined. This includes also work and weld seam preparation and the positioning of the parts being welded. In addition: Repairing and cleaning of welds, the correction of welding defects, the removal of spatter and straightening due to thermal distortion are also contributing factors.
Our Wobble Laser Welding Technology results in a minimal 70% energy reduction compared to other welding technologies.
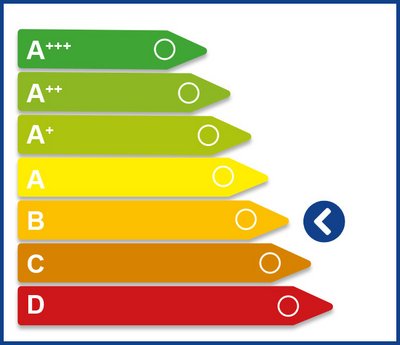
Metal arc welding (TIG/TAG)
Class B
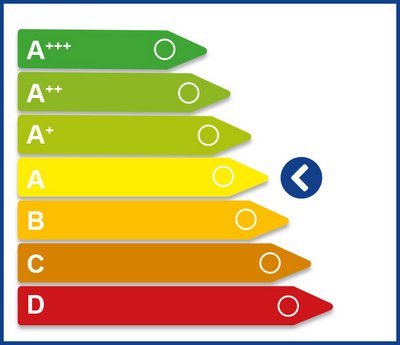
Metal Plasma Beam Welding
Class A
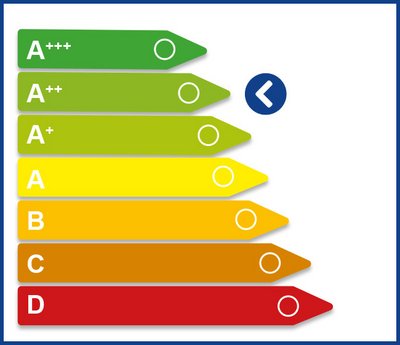
LASER WOBBLE WELDING
Class A++
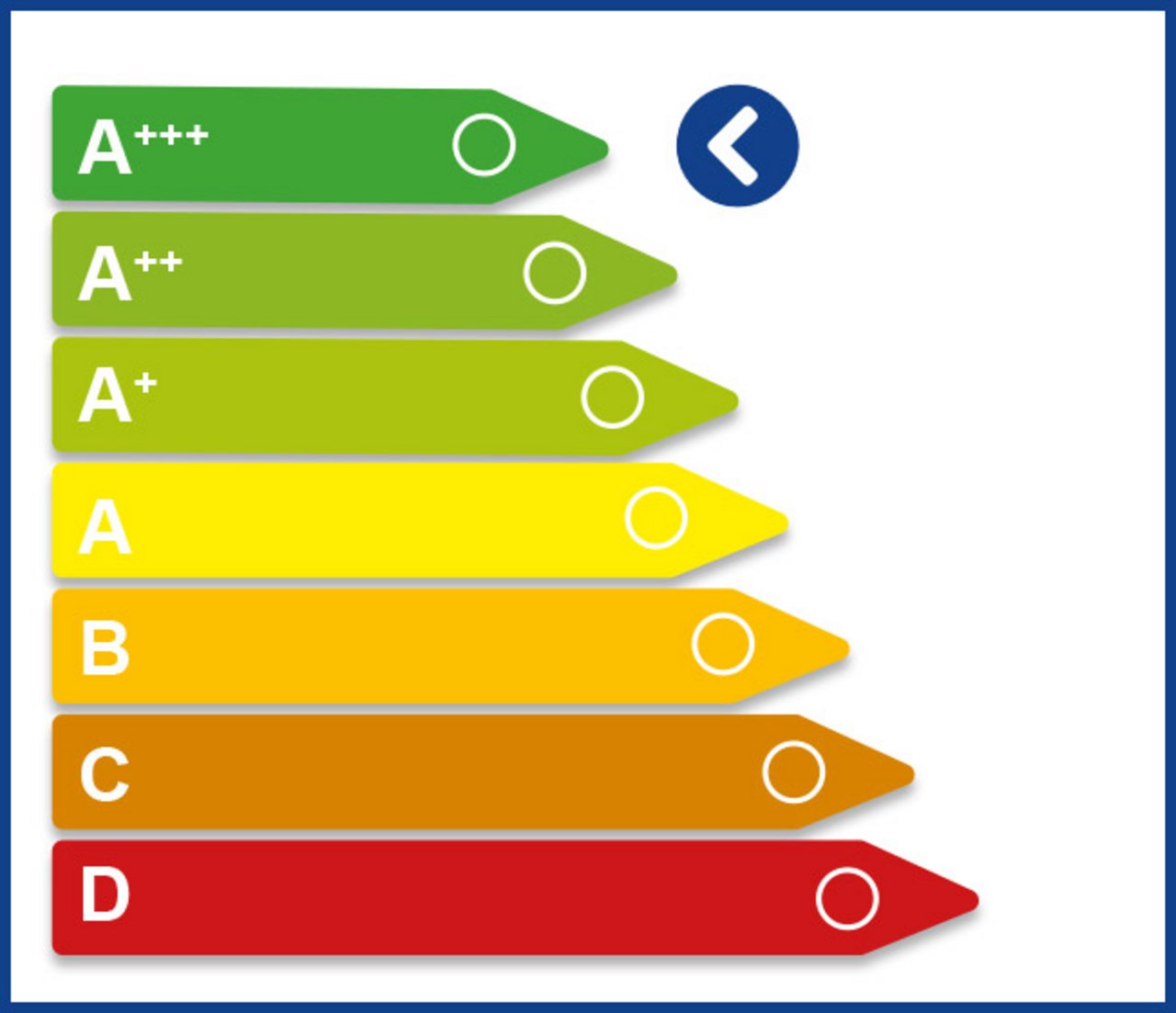
PhotonWeld LASER WOBBLE WELDING
Class A+++
Sustainable Manufacturing
Green welding: good for the environment and the bottom line
Environmental impacts of welding
The welding process directly generates two broad categories of detrimental byproducts: toxic emissions and process heat. These byproducts most often affect the welder’s immediate environment rather than the community surrounding a welding shop or plant. Emissions include minute particles, including nano-sized particles, of metal oxides and gases like carbon monoxide, ozone and various nitrogen oxides.
These immediate and direct negative byproducts are not the only components of the welding process that generate environmental damage and negatively impact sustainability. Process inputs like electrical energy, filler material, consumable electrodes and shielding gas have direct costs for the company and less-obvious environmental costs. Generating electricity most often requires consumption of natural resources that must be mined.
Greener ways to weld
Different welding techniques generate different amounts and kinds of pollutants, so selection of technique has an impact on environmental impact. Wobble Laser Welding techniques create less pollution because they eliminate the need for fillers or flux and do almost not produce dangerous fumes. Another Big advantage is the huge reduction of energy consumption. Laser Welding reduces the energy consumption with more than70% sometimes!
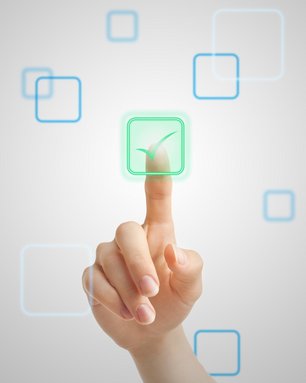
Reversing climate change processes by improving the energy performance of industrial Processes
Metal Industry currently account for a serious part of the European primary energy demand and for an equal part of Europe’s CO2 emissions.
The total Metal industry are among the biggest consumers of energy and the largest contributors to global greenhouse emissions, ahead of transport, agriculture and other industrial processes. In response the EU has set a range of energy targets by 2030. By improving the energy efficiency, we can reduce total EU energy consumption and help to attain long-term objectives.
(Sources: EC, EU Energy Figures – “Statistical Pocket Book 2019” and Glazing Potential – Energy Savings & CO2 Emission Reduction, Glass for Europe)