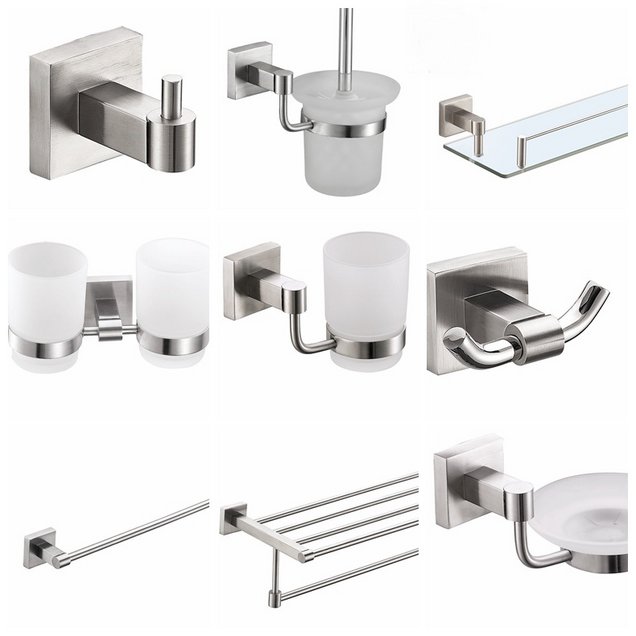
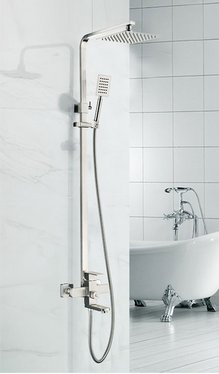
Laser welding solves problems encountered in stainless steel sanitary products
Modern stainless steel sanitary ware manufacturing becomes increasingly demanding on welding strength and appearance effects, especially components with high added value and extremely high welding quality requirements. It’s better that they can be completed without or with minimal subsequent processing. However, traditional welding methods will inevitably cause problems such as distortion of the workpiece due to the extreme heat input. In order to compensate for the problem of workpiece deformation appearing with traditional welding, a large number of follow-up processing methods are required, thereby drastically increasing costs.
In addition, due to the fast welding speed and large welding aspect ratio of laser wobble welding, welding efficiency and stability can be greatly improved. Therefore, laser wobble welding becomes more and more popular in the manufacturing of sanitary ware, stainless steel, glasses, mobile power and other industries. Due to the extremely low heat input during laser welding, the amount of deformation after welding is very small, and a very beautiful welding surface effect can be obtained, with few subsequent welding treatments, which can greatly reduce or eliminate the labor cost of the huge polishing and leveling process. Laser welding is carried out in a closed safety shield and equipped with an automatic dust extraction device. While ensuring the health and safety of employees, it can also maintain a clean and tidy working environment in the workshop.
Our wobble laser welding machines can handle the welding of tee pipes or shower heads. The heat-affected zone is small, and there is no problem of workpiece deformation. The welding surface is smooth and uniform. High-quality welding will reduce the follow-up workload, thereby reducing production costs and improving production efficiency.
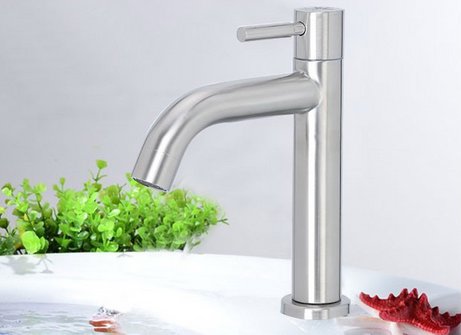
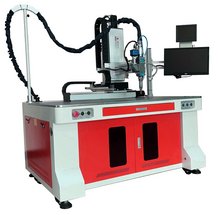