Fiber laserlassen
Fiberlaserlassen is, net als andere laserbewerkingsmethoden, een contactloze technologie met een beperkte, door warmte beïnvloede zone (HAZ), daarom is de technologie een voorkeursmethode voor het lassen van delicate producten met hoge snelheden. Laserlassen is ook een meer herhaalbaar en consistent proces dan andere lasmethoden, en is in staat om zeer sterke verbindingen te produceren zonder dat er vulmateriaal, vloeimiddel, voorbereiding of secundaire reinigings- en afwerkingsprocessen nodig zijn. Fiberlaserlassen heeft het mogelijk gemaakt dat veel toepassingen, zoals energieopslag met lithium-ionbatterijen en implanteerbare medische apparaten, op extreme schaal kunnen worden vervaardigd, tegen veel lagere kosten, met grotere consistentie, met grotere snelheden en met veel minder verspilling en kwaliteitscontrole problemen. Bovendien is een productieproces voor laserlassen veel betrouwbaarder dan andere lastechnologieën, aangezien de nieuwste laserlasmachines weinig tot geen onderhoud vergen en vrijwel geen uitvaltijd.
A weld can be created either as an individual spot or a seam weld.
The laser output that creates these welds can be achieved in one of two ways:
A pulsed laser produces a series of pulses, discrete packets of energy, at a certain pulse width and frequency until stopped. The “pulsed” descriptor refers to a laser that can produce a peak power that is greater than its average power.
A continuous wave (CW) laser produces extended output – the laser remains on continuously until stopped.
For example, a 25 W pulsed Nd:YAG laser can produce peak powers of up to 5 kW for a few milliseconds. This means it can produce a spot weld that would require a CW laser sized at 5 kW! With pulsed lasers a seam weld is created by a series of overlapping spot welds. For a continuous weld the laser remains on for the duration of the seam. A CW laser can also produce discrete pulses of laser light – known as gated or modulated output. In this case the CW laser peak power does not exceed the laser’s rated average power.
An Nd-YAG laser operates only in pulsed mode
Diode lasers operate in continuous wave
Fiber lasers can operate in both modes.
Choosing when to use pulsed, continuous wave, or modulated output is determined by the specific application. Spot welding typically uses pulsed operation. For seam welding, the selection is made based on heat input and cycle time. For instance, when seam welding an implantable device, a pulsed laser is used to minimize heat input and maintain a uniform weld around a complex geometry with varying welding speeds. In contrast, for airbag initiators, welding at high speed using CW operation is
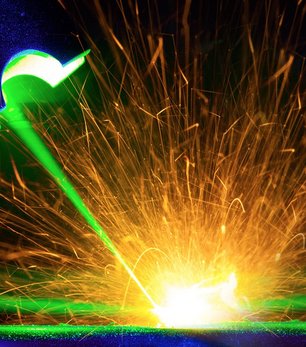
Laser welding does not operate on the same principles as other types of welding like TIG, MIG, MAG,..
Laser welding uses a beam of light, instead of electricity, to join two pieces of metal together through a melting and cooling process.
Another key difference with laser welding is the intensity and ability to focus the heat source: the laser. The much higher, focused heat than, say, the electricity of a MIG welder or TIG welder, means that the weld occurs much more quickly. What’s more, the ability to narrowly pinpoint the weld area leads to much greater precision and more accurate and attractive weld joints.
What does this mean for you?
- Higher speeds: till 10x faster than MIG welding, and till 40x faster than TIG welding.
- Minimal/no finishing: The accuracy of the laser welding process means that little to no grinding or finishing is needed.
- Visually superior: Laser welding is ideal for straight line joints in furniture and other consumer products, since there is a much smaller heat-affected zone and a much tighter weld.
- Greater strength: A smaller heat-affected zone also means less weakening of the material.
So when wouldn’t you want to use laser welding? Thicker materials and parts where the weld joint construction does not allow the fit-up to be consistently maintained generally are not good candidates for laser welding.
Laser welding can be divided into the following processes:
Heat conduction welding and Keyhole (deep penetration) welding
Fiber laser welding is a high power density process that provides a unique welding capability to maximize penetration with minimal heat input. The weld is formed as the intense laser light rapidly heats the material – typically in fractions of milliseconds. There are two types of welds, based on the power density contained within the focus spot size: conduction modeand penetration/keyhole mode. A third type named as transition keyhole mode is the combination of the conduction mode and penetration/keyhole mode.
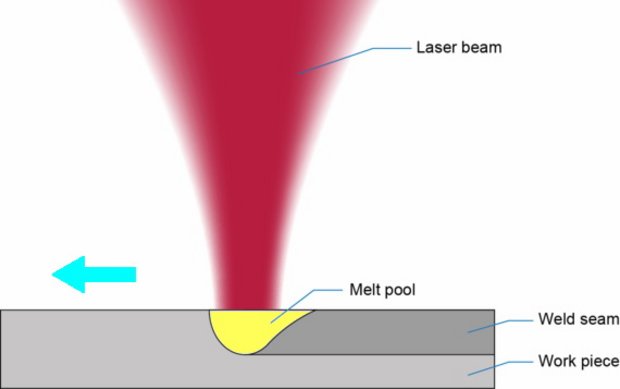
Conduction mode laser welding
Conduction mode welding is performed at low energy density, typically around 0.5 MW/cm², forming a weld nugget that is shallow and wide. The heat to create the weld into the material occurs by conduction from the surface. Typically this can be used for applications that require an aesthetic weld or when particulates are a concern, such as certain battery sealing applications.
Heat conduction welding is a laser welding method that features a low power output laser beam. This makes for a penetration depth of no more than 1 to 2 mm. With the ability to handle a relatively wide power range, heat conduction welding can be adjusted to the ideal power level, and the shallow penetration makes it possible to weld materials that are susceptible to heat effects under optimal conditions.
This welding type is used for butt joints, lap joints, and other welding applications for thin plates, and can also be used for welding hermetic seals and other seals. Heat conduction welding is also suitable for volatile alloys such as magnesium and zinc, for which keyhole (deep penetration) welding is not suitable.
Transition mode laser welding
Transition mode laser welding occurs at medium power density, around 1 MW/cm2, and results in more penetration than conduction mode due to the creation of what is known as the “keyhole.” The keyhole is a column of vaporized metal that extends into the material; its diameter is much smaller than the weld width and is sustained against the forces of the surrounding molten material by vapor pressure. The depth of the keyhole into the material is controlled by power density and time. Because the optical density of the keyhole is low it acts as a conduit to deliver the laser power into the material.
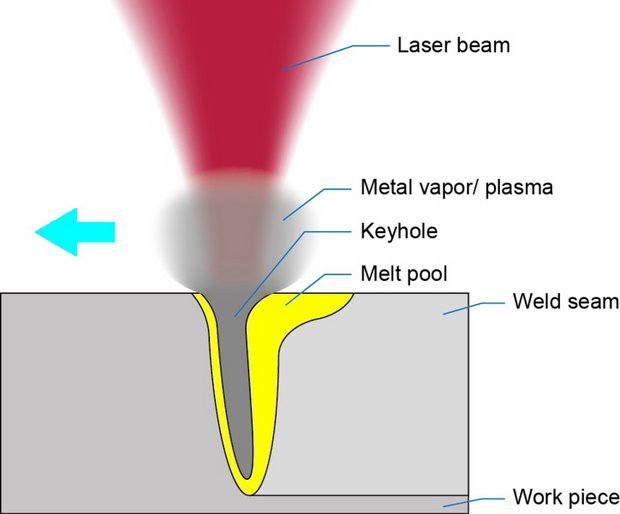
Keyhole mode laser welding or penetration mode laser welding
Keyhole or penetration mode welding – Increasing the peak power density beyond 1.5MW/cm2 shifts the weld to keyhole mode, which is characterized by deep narrow welds with an aspect ratio greater than 1.5. The penetration depth rapidly increases when the peak power density is beyond 1 MW/cm2, transitioning the weld mode from conduction to keyhole/penetration welding.
Penetration or keyhole mode welding is characterized by narrow welds. This direct delivery of laser power into the material maximizes weld depth and minimizes the heat into the material, reducing the heat affected zone and part distortion. In this keyhole mode, the weld can be either completed at very high speeds – in excess of 500mm per second with small penetration typically under 0.5 mm – or at lower speed, with deep penetration up to 12 mm.
Keyhole welding (deep penetration welding) uses a high power output laser beam for high-speed welding. The narrow, deep penetration allows for uniform welding of internal structures. Because the heat-affected zone is very small, distortion of the base material, due to the heat from the welding, will be minimized.
This method is suitable for applications requiring deep penetration or when welding multiple base materials stacked together (including for butts, corners, Ts, laps, and flange joints).
Procesparameters voor laserlassen
De sleutel tot succes
Vermogensdichtheid
De vermogensdichtheid is een van de meest kritische parameters bij de laserbewerking. Met een hogere vermogensdichtheid kan de oppervlaktelaag worden verwarmd tot het kookpunt in een tijdbereik uitgedrukt in microsecondes, wat resulteert in een grote hoeveelheid verdamping.
Om die reden is een hoge vermogensdichtheid voordelig voor materiaalverwijdering zoals ponsen, snijden en graveren. Voor lagere vermogensdichtheden bereikt de oppervlaktetemperatuur het kookpunt en duurt het slechts milliseconden. Voordat de oppervlaktelaag wordt verdampt, bereikt de onderste laag het smeltpunt en is het gemakkelijk om een goede fusie te vormen.
Daarom is in geleidingslaserlassen de machtsdichtheid in het bereik van 10^4~10^6W/CM^2.
De golfvorm van de laserpuls
Laserpulsgolfvormen zijn een belangrijk aandachtspunt bij het laserlassen, vooral bij het plaatlassen. Wanneer een laserstraal met een hoge intensiteit op het oppervlak van het materiaal valt, wordt het metaaloppervlak gereflecteerd door 60 tot 98% van de laserenergie en zal het reflectievermogen variëren met de oppervlaktetemperatuur. Tijdens een laserpulsactie verandert het reflectievermogen van het metaal sterk.
Laserpulsbreedte
Pulsbreedte is een van de belangrijke parameters van het pulslaserlassen. Het is een belangrijke factor die verschilt van materiaalverwijdering en materiaalsmelting, en is ook een belangrijke paramter die de kosten en het volume van de verwerkingsapparatuur bepaalt.
Het effect van defocushoeveelheid op de laskwaliteit
Bij laserlassen is meestal een bepaalde mate van defocus nodig, omdat de vermogensdichtheid in het midden van de plek bij de laserfocus te hoog is en het daardoor gemakkelijk is om te verdampen in gaten. De verdeling van de vermogensdichtheid is relatief gelijkmatig over de vlakken die de laserfocus verlaten.
Er zijn twee manieren van defocussen: positieve defocus en negatieve defocus.
Het brandvlak bevindt zich boven het werkstuk bij positieve defocus en omgekeerd bij negatieve defocus. Volgens de theorie van de geometrische optiek is, bij een gelijke afstand tussen het positieve en negatieve defocusvlak en het lasvlak, de vermogensdichtheid op het betreffende vlak ongeveer gelijk, maar is de vorm van het verkregen smeltbad anders. In het geval van negatieve defocus kan een grotere indringing worden bereikt, hetgeen samenhangt met de vorming van het smeltbad.
Experimenten hebben aangetoond dat het materiaal reeds na 50~200μs begint te smelten, dit vormt de vloeibare fase van het metaal waarbij er een gedeeltelijke verdamping optreedt. Dit vormt stoom dat zich aan een hoge snelheid verplaatst en door de hoge druk een verblindend wit licht uitstraalt. Tegelijkertijd, beweegt de hoge concentratiedamp het vloeibare metaal naar de rand van het bad en vormt een holte in het centrum van het bad.
Wanneer er een negatieve defocus plaatsvindt, de interne machtsdichtheid van het materiaal is hierbij hoger dan dat van de oppervlakte waardoor het gemakkelijk is om een sterke smelting en verdamping te vormen, wordt de energie naar het diepere deel van het materiaal overgebracht. Daarom worden er in praktische toepassingen, wanneer de penetratiediepte groot moet zijn, negatieve defocus gebruikt; bij het lassen van dunne materialen wordt de voorkeur gegeven aan positieve defocus.
Lassnelheid
Als de lassnelheid te laag is, is de warmte-inbreng te groot, waardoor het werkstuk doorbrandt. Als de lassnelheid te hoog is, is de warmte-inbreng te klein, waardoor het werkstuk niet goed kan worden gelast.
Industriële laserlassystemen
Industrieel laserlassen heeft in de loop der jaren een enorme impact gehad in de machinegereedschapsindustrie en is het antwoord geworden op veel problemen die worden veroorzaakt door traditionele lasmethoden. Veel metaalbewerkingsbedrijven zijn vanwege deze voordelen overgestapt op laserpunt- en lasernaadlassen. Automatisering, hoge lassnelheden en contactloze verwerking helpen gebruikers van laserlassen om zeer snel economische voordelen te behalen.
Omdat laserlassen pure, geconcentreerde energie produceert, creëert het diepere lassen terwijl een hoge productie-output overblijft. Dit is een van de vele redenen waarom laserpunt- en naadlassystemen worden gebruikt in de productie in deze industrie. Artikelen die we elke dag gebruiken in onze gadgets, elektronica en onderdelen hebben laserlastechnologie ondergaan tijdens hun productie.
Laserpuntlassen en lasernaadlassen
Laserpuntlassen, lasernaadlassen en direct lassen zijn zeer nuttige en enigszins verschillende toepassingen van laserlastechnologie. Laserpunt- en naadlassen verwijzen naar lasfuncties die op een enkel punt of langs een lijn worden toegepast. Door een laserlassysteem in te stellen op een hoge snelheid en een extreem smalle lasgeometrie, kan de laserlasser extreem fijn puntlassen produceren. U kunt het systeem ook aanpassen om in de continue golfmodus te lassen, waarbij u met een vermogen van meerdere kilowatts lassen. De ideale lasersnelheid voor laserpunt- of naadlasprojecten varieert afhankelijk van het specifieke lasermodel, het laservermogen en het materiaal dat wordt gelaserd.