Fiber Laser Wobble las opplossingen vinden we nu reeds overal en er komen er nog heel veel meer aan!
Onze Fiber Laser Wobble las oplossingen openen nu gigantisch veel deuren!
Laserlassen mag niet als 'niet-traditioneel' worden beschouwd, gezien de vele toepassingen gedurende vele jaren. Nu met fiberlaserlassen, en specifiek met fiberlaser wiebellassen, zijn er overal nieuwe producttoepassingen - in elektronische pakketten, medische apparatuur, de voertuigen waarin we rijden, het vliegtuig waarin we vliegen, in procesapparatuur en sensoren. De lijst is bijna eindeloos. De meeste van de eerdere beperkingen van laserlassen bestaan niet meer of kunnen gemakkelijk worden overwonnen.
Hoewel fiberlaserlassen in eerste instantie intimiderend kan zijn, is herhaaldelijk aangetoond dat het nieuwe productontwerpen mogelijk maakt met aanzienlijke verbeteringen in kosten, kwaliteit en prestaties. Met ons beschikbaar technisch personeel die de nieuwe toepassingen ontwikkelen, bieden we nu ook gebruiksklare oplossingen. Dat omvat niet alleen de machine, maar ook het fixeren van de toorts en het gemakkelijk leren werken met deze nieuwe laserlas technieken.
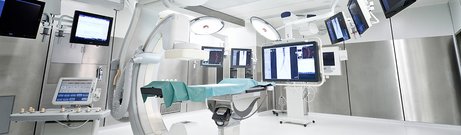
Medical Industry
Products within the medical industry require the highest levels of precision. You have to meet the highest quality demands. The size of many medical devices and products is continually decreasing, and lasers are perfectly suited for creating equally minute weld seams. Even in complicated areas, laser weld spots and seams can easily be generated to provide sterile surfaces with no post-processing.
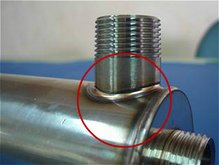
Hermetic Welding of Electronic Packages
Hermetic sealing electronics in medical devices, such as pacemakers, and other electronic products has made fiber laser welding the process of choice for applications requiring the highest reliability. A recent advance in the hermetic welding process has addressed concerns about laser welding and the end point of the weld, a critical location point in completing the hermetic seal. Previous laser welding techniques resulted in a depression at the end point when the laser beam is turned off, even when ramping down the laser power. Advanced control of the laser beam eliminates the depression in both thin and deep penetration welds. The result is consistent geometry and lack of porosity at the end point with improved cosmetic appearance and more reliable hermeticity.
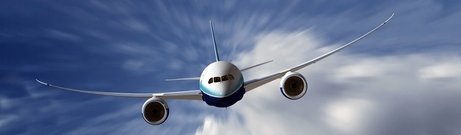
Aerospace Industry
The capabilities of laser welding have proven to play an integral role in the production of aerospace materials and parts. Examples of this would be in airport security procedures or flight components. The need for maximum precision leaves no room for error and laser welding offers high levels of accuracy. Therefore, making it a favourable technique for an excellent standard of work that meets specifications and regulations.
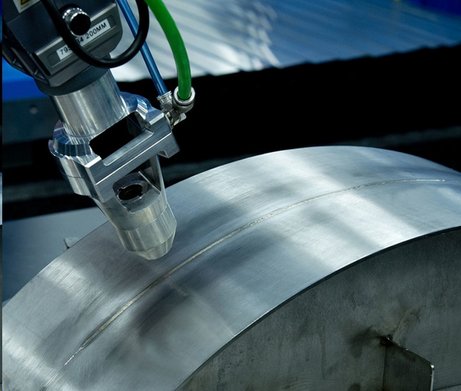
Aerospace Welding
Fiber laser welding high temperature nickel-based aerospace components ensures a consistent and robust joint.
Welds that meet the geometry and quality requirements for aerospace applications are readily produced.
Laser welding nickel and titanium-based aerospace alloys requires control of the weld geometry and weld microstructure, including minimizing porosity and controlling grain size. In many aerospace applications, the fatigue properties of the weld are a critical design criteria. For this reason, designers nearly always specify that the weld surfaces be convex, or slightly crowned, to create a reinforcement of the weld.
To achieve this, a 1.2 mm diameter filler wire is used in the automated process or you use a wobble welding head. Addition of the filler wire to a butt joint leads to a consistent crown on both the top and bottom weld bead. The selection of the alloy of the wire also contributes to the weld’s mechanical properties by ensuring a sound microstructure of the weld.
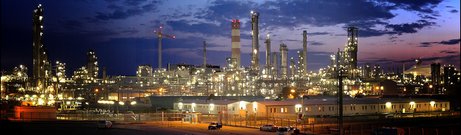
Gas and Oil Industry Repairs
With Laser welding Technology rapidly customers within the Oil and Gas industry, changing over to laser welding services for both repairs, modifications and concept work. the result is faster, better and cheaper.
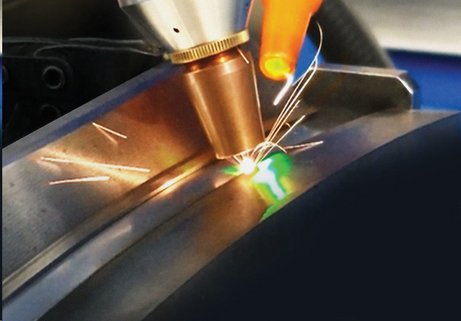
Precision Machined Component Welding
Seals used in ships and chemical refineries and for pharmaceutical manufacturing were originally TIG welded. Because of their use in sensitive environments, these components are precision machined and ground from high temperature and chemical resistant nickel-based alloy material. Lot sizes are usually small and the number of setups are many.
The assembly of these components has been improved using fiber laser welding.
Justification to replace the earlier robotic arc welding process with fiber laser welding using a four axis cartesian coordinate machine tool were:
- consistently higher quality of the laser welds,
- ease of changeover from one component configuration to another that reduced setup time,
- automating the laser welding process using a four-axis CNC laser machine improved throughput while decreasing assembly costs.

Food and Beverage Industry
You must have a high-quality weld and surface finish within the food and beverage industry, due to the hygienic requirements. If the weld integrity or surface finish isn’t perfect and faultless, the consequences could be both expensive and unsanitary. Even the smallest niche left by a weld can allow the product to get trapped and form bacteria which could potentially contaminate the food.
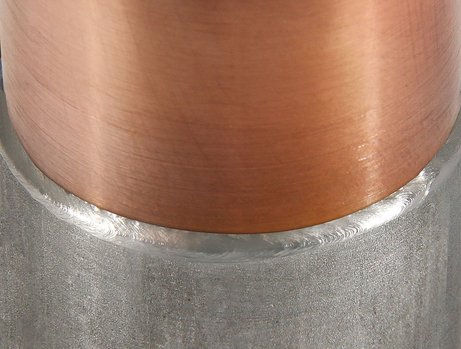
Dissimilar Metal Welding
Welding of Dissimilar Metal Sheet Metal Components
The ability to create products using different metals and alloys greatly increases both design and production flexibility. Optimizing properties such as corrosion, wear and heat resistance of the finished product while managing its cost, is a common motivation for dissimilar metal welding.
Joining stainless steel and zinc coated (galvanized) steel is a one example. Because of their excellent corrosion resistance, both 304 stainless steel and zinc coated carbon steel have found widespread use in applications as diverse as kitchen appliances and aeronautical components.
The process presents some special challenges, particularly since the zinc coating can present serious problems with weld porosity. During the welding process, the energy that melts steel and stainless steel will vaporize the zinc at approximately 900⁰C, which is significantly lower than the melting point of the stainless steel.
The low boiling (vaporization) point of zinc causes a vapor to form during the keyhole welding process. In seeking to escape the molten metal, the zinc vapor may become trapped in the solidifying weld pool resulting in excessive weld porosity. In some cases, the zinc vapor will escape as the metal is solidifying creating blowholes or roughness of the weld surface.
With proper joint design and selection of laser process parameters, cosmetic and mechanically sound welds are readily produced.
Laserlassen in Belgie - laserlassen in Nederland - Laser welding in the UK - Soudage laser en France - Soudage laser en Belgique - Soudage laser au Luxembourg - Laserschweißen in Deutschland - Laserschweißen in Österreich - Soldadura láser en españa - Saldatura laser in italia - Soldadura a laser em portugal - Laser welding in ireland - Lasersvejsning i danmark - Sudarea cu laser în Romania - Soudage laser en Suisse - Laserschweißen in der Schweiz - Laser bidezko soldadura espainian - Laser bidezko soldadura espainian - Laserové svařování v česku - Laserové zváranie na slovensku - Lasersko varjenje v sloveniji - Lasersko zavarivanje u hrvatskoj - Lasersko zavarivanje u bosni - Ласерско заваривање у Србији - Лазерно заваряване в българия - Συγκόλληση με λέιζερ στην Ελλάδα - Spawanie laserowe w Polsce - Лазерне зварювання в Україні - Лазерная сварка в украине - Лазерная зварка ў Беларусі - Laserhitsaus Suomessa - Lasersvetsning i sverige - Lasersveising i norge - Laser welding in united states - Laser welding in canada - Soudage au laser au Canada - Türkiye'de Lazer Kaynak - ריתוך לייזר בישראל