The aerospace industry is a heavy user of fiber laser welding
The aerospace industry is perhaps one of the most commercially important in the modern age. It has had a profound impact on many other areas of society, including travel, business and the transport of goods and services. Not to mention its role in the military or even space exploration. From carrying hundreds of people and thousands of kilograms in weight to reaching new corners of space, it is fair to say that the aircraft that are designed in this industry undergo much pressure and therefore need to be manufactured to precise specifications.
“Aerospace” is a rather broad term which has come to encompass many different facets as we examined above. It involves everything from the design through to the sale of aircraft, and everything from short haul travel to travel beyond the atmosphere. Given this, there are hundreds of thousands of businesses and people involved in this fast-paced sector. It’s not surprising that it’s become such a valuable sector too.
Around eight million people fly every single day, meaning that passengers will take over three billion flights each year.
With such a huge amount of travel that involves so many people, the aerospace industry has always been once that focuses on high quality and safety. There can be no room for error, and as the industry has continued to adapt, so too has the methodologies and processes that it utilises. One of these is laser welding.
To build machines that will not only last, but will also work well under such stress, there is a heavy reliance on modern, safe and high-quality processes. Fiber laser welding is just one such process, but plays a crucial role within this sector. One of the biggest reasons that laser welding has grown in prominence with aircraft manufacturing and maintenance is their ability to work with a variety of materials. There are many materials involved within this industry, not to mention a variety of metals.
Laser welding setups are great at working with a high degree of materials, including the welding together of different substances. For example, dissimilar metal welding is a process that is needed often within this industry. But, one reason that our lasers have become such a popular choice is their ability to work with reflective metals, such as aluminium and copper. Other types of lasers, such as the gas laser, can struggle with this, given the reflective nature of the materials. Many different types of metals are used in the aerospace industry.
One of the most comm.on applications for fiber laser welding in this sector is for the creation of strong weld joints between turbine components. Traditionally, methods such as vacuum brazing were used, but this was expensive and took many, many hours. Welding using a fiber laser, however, has lower rework costs, is much quicker, parts don’t need to be specially designed with a gap and no fixtures are needed to hold the various parts in the right position
Aerospace Laser Welding
Laser welding precision
The capabilities of Aerospace Laser Welding has proven to play an integral role in the production of aerospace materials and parts. Whether it be airport security procedures or flight components, the need for maximum precision leaves no room for error. Aerospace Laser welding offers you high levels of accuracy. Therefore, making it a favourable technique for a consistently excellent standard of work. You can meet the strict specifications and regulations with this technique.
How is it better than traditional methods?
One of the major advantages of laser welding is the strength and durability of the finished product. Especially in the aerospace industry. High strength welds are essential to the manufacture of parts because of the necessity to achieve maximum effectiveness. A low heat input noticeably reduces imperfections in the material. This is because the heat affected area is incredibly minimal /non existent at all and the surrounding material is not annealed. The consistency and precision of laser welding remain unmatched by traditional welding methods. You can therefore weld with a more precise and versatile process. In addition, unlike more traditional welding techniques, it’s possible to weld various materials that are not similar to one another.
The beauty of Aerospace Laser Welding is the fact that it is so minimally intrusive. This in incredibly important within the Airport Security spectrum and within finding contraband. Laser Precision ensures that within this important field, that no mistakes are made.
Aerospace manufacturers are increasingly turning to fibre lasers to resolve their manufacturing challenges.
Fibre lasers are very stable and reliable instruments, which offer optimal beam quality for material processing applications where precision is important.
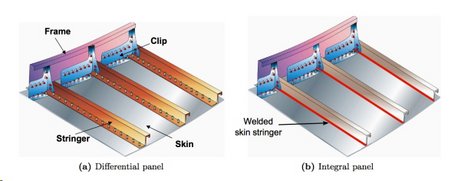
LASER BEAM WELDING OF AIRFRAME STRUCTURES
Over the past 15 years the major airframe manufacturers around the world have been investigating alternatives to riveted airframe structures. This development work has been driven by the opportunity to save weight by the removal of overlapping aluminium skins and hundreds of thousands of rivets.
Laser welding of aluminium materials for airframe manufacture is growing in interest, and the large aerospace companies are investing more time in this technology in an effort to replace riveting wherever possible.
Laser beam wobble welding was adopted for the joining of fuel tanks with spectacular results in terms of improved joint efficiency, strength, reduced rework and substantial cost savings. Its use in commercial aircraft manufacture has been slower to develop, but is starting to increase due to the weight and cost savings associated with its use.
Laser welding of 2XXX aluminium alloys would be the preferred route, but these alloys can be crack sensitive when welded. It is possible to use lower strength 6XXX alloys for lower fuselage panels, and this material is much easier to weld. Al-Mg-Sc alloys are now being considered for upper fuselage panels where higher strength is required.
Aerospace welding
Fiber laser welding nickel and titanium-based aerospace alloys requires control of the weld geometry and weld microstructure, including minimizing porosity and controlling grain size. In many aerospace applications, the fatigue properties of the weld are critical design criteria. For this reason, design engineers nearly always specify that the weld surfaces be convex, or slightly crowned, to create a reinforcement of the weld. To achieve this, a 0.8~1.2-mm-dia. filler wire is used in the automated process. Addition of the filler wire to a butt joint leads to a consistent crown on the top and bottom weld bead. The selection of the alloy of the wire also contributes to the weld’s mechanical properties by ensuring a sound microstructure of the weld.