Wobble welding advantages and benefits
Wobble welding technology allows to skip the filler material while achieving a high quality welding seam.
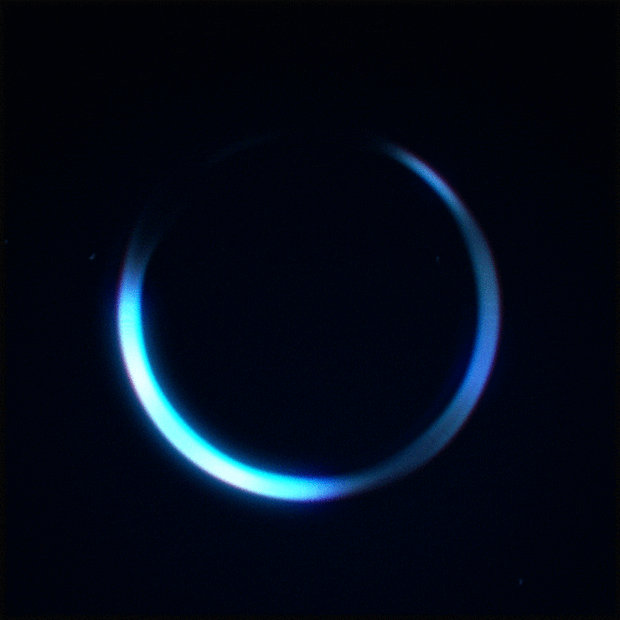
The wobble laser welding method produces a superior weld by greatly reducing imperfections, increasing consistency, reducing material cost and providing more tolerance for process variables.
Benefits of wobble fiber laser welding
Above all, the use of laser welding for metal parts improves productivity by reducing the time spent on welding and straightening the welded parts and allows greater freedom in the designing of parts (simpler assemblies). Laser welding also helps make savings by reducing production costs and the materials consumed by the welding process. This welding method also affects the quality of the assembly by offering mechanical strength that is at least equal to that of the base material, and by reducing the part deformation rate. Laser welding is also an excellent solution for joining subassemblies of dissimilar parts or treated parts (carbonitrided, case hardened, etc.).
Benefits
- Welding productivity can increase by up to 800 %
- Reproducible process
- Reduction or even elimination of the time for straightening welded pieces
- Overall reduction of production costs
- Mechanical resistance at least equivalent to that of the base metal
- Reduction of welding consumables
- Great freedom in the designing of parts
- Fume and smoke drastically reduced
- Few splatters and flames
- Drastic reduction of post-processing (cleaning, grinding,...)
- Welding of dissimilar materials (steel to cast iron, stainless steel to Inconel, etc.)
- Welding of precious materials
- Welding close to delicate components
- Welding time is reduced to a tenth
- Reduced deformation of parts
- Welding of parts with limited accessibility
- Process that can be automated
- Assembly with no filler metal
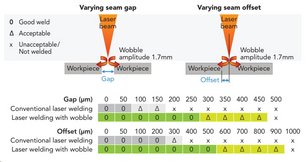
Wobble Laser Torch Welding - Seam Gap and Seam Offset
A factor of 3~5 increase in both process parameters can be achieved compared to conventional laser welding without Wobbling!
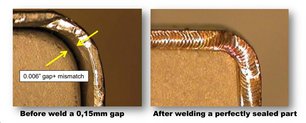
Seam Sealing Butt Weld with Loose tolerance
Bridge wide gaps with our Wobble6-PRO+
- Larger Wobbling Spot Size helps bridging bigger gaps
- The required tolerance for fit-up is reduced
- The lower tolerances needed reduce the machining costs
- Non tolerance parts can still be used : less scrap, less losses = big savings
- Maximum yield and quality of welded part
Laser stir welding (wobble welding) involves the manipulation of the laser beam to provide hydrodynamic stirring and subsequent healing of the keyhole.
To achieve the wobble method, a fixed laser is optically manipulated with attachments, such as our wobble head, that allow the laser to wobble to a programmed pattern down the seam of the weld. The wobble method produces a superior weld by greatly reducing imperfections, increasing consistency, reducing material cost and providing more tolerance for process variables.
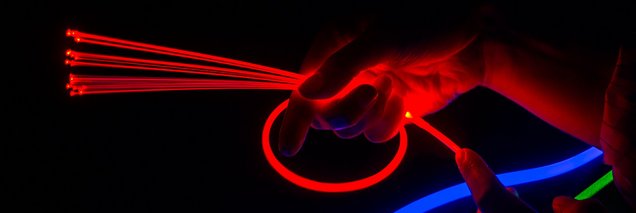
FIBER LASER BENEFITS
The fiber laser has the following benefits and advantages:
1. When compared to CO2 laser beam, it provides simplified beam delivery using fiber-optic cables without having to deal with alignment of mirrors.
2. It is absorbed more by metals, especially good conductors, and is less absorbed by plasma vapours formed above the weld pool.
3. Fiber lasers give increased power intensity owing to its ability to be focussed to smaller sizes.
4. Light can be easily transferred to a movable workpiece because it is already present in a flexible fibre. This fact is extremely useful for laser cutting and welding.
5. Optical fibers can be several kilometers long, hence fiber lasers are capable of providing extremely high power output.
6. Large surface area to volume ratio accounts for continuous power output due to efficient cooling.
7. Fiber lasers are very stable with respect to temperature and vibrations. Fibers protects the optical path from thermal distortion.
8. Better beam quality also give cleaner welds.
9. They have very low ownership and maintenance costs and also use low electricity. These factors allow deeper penetration and faster welding speeds in comparison to other welding processes