Precision machined laser welded Seals
Seals used in petro-chemical refineries were originally TIG welded. Because of their use in sensitive environments, these components are precision machined and ground from high-temperature and chemical-resistant nickel-based alloy material. Lot sizes are usually small and the number of setups is many.
The assembly of these components has been improved using fiber laser welding. Justification to replace the earlier robotic arc welding process with fiber laser welding using a four-axis cartesian coordinate machine tool includes consistently higher quality of the laser welds, ease of changeover from one component configuration to another reducing setup time, and improved throughput and decreased assembly costs by automating the laser welding process using a four-axis CNC laser machine.
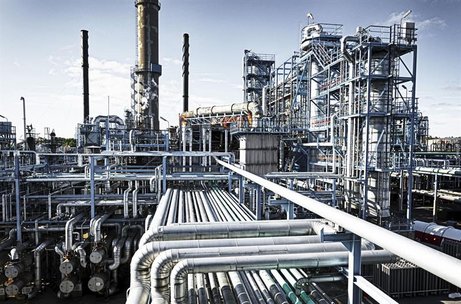
Petro-chemical industrial plants
Laser Welding in Precision tubing
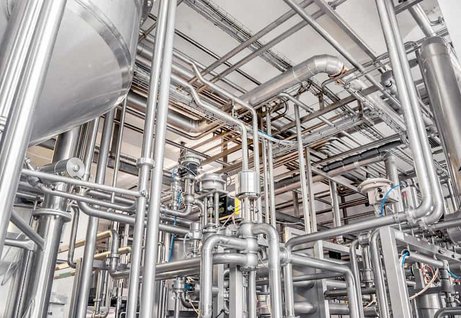
Laser-welded tube quality
Although induction welding systems perform sometimes welding faster than lasers can, big heat is deposited into more of material, resulting in a relatively slow cooling rate and a huge energy consumption compared to laser welding. The fiber laser heats only a very narrow line along the tube, enabling a much higher cooling rate. This can be an advantage except when high-strength steels are joined. Nowdays every tube maker switch over to use the laser welding system for the production of stainless steel and mild steel tubes. The high cooling rate in the heat-affected zone next to the molten zone of the weld seam means a risk of cracking during shaping, as the produced tubes have to be shaped extensively. With use of our wobble technology, we are able to reduce this cracking risk with more than 80%.