Medical Laser Welding
Welds in medical devices and instruments are mission critical: a failure could mean a life!
Products within the medical industry require the highest levels of precision. It is incredibly important that they meet the highest quality demands. The size of many medical devices and products are continually decreasing. This is where lasers are perfect as they are perfectly suited for creating equally minute weld seams. Even in complicated areas, laser weld spots and seams can easily be generated to provide sterile surfaces with no post-processing.
Medical laser welding benefits
As laser welding is non-contact, it ensures that minimal / no heat damage is caused to the surrounding material. This is great for the medical industry as it is the most effective, non-intrusive way to weld the tools. Therefore, ensuring no damage is one to them. As precision is key to this industry, laser welding is also key. In addition, as it is a precise means of manufacturing, it is a quick, way to minimise economic spending. It also provides both quality and quantity in production.
The high weld integrity achieved with laser-welded joints makes them suited for high-temperature sterilisation. Additionally, the limited heat affected area ensures that surrounding material is not annealed and weakened. A wide variety of metals can be laser welded, including alloys, and there are no filler materials added during the processing. This removes any potential biocompatibility issues for products such as implants.
How is it used in the medical industry?
Just a few examples of medical devices that can be created with the aid of laser welding include:
- Pacemakers
- Hearing Aids
- Prosthetics
- Catheters
- Defibrillators
You need ultimate precision when dealing with products from the medical industry. There is simply no room for mistake. Furthermore, it is pivotal that they meet the highest quality demands. Even in complicated areas, laser weld spots and seams can easily be generated to provide sterile surfaces with no post-processing.
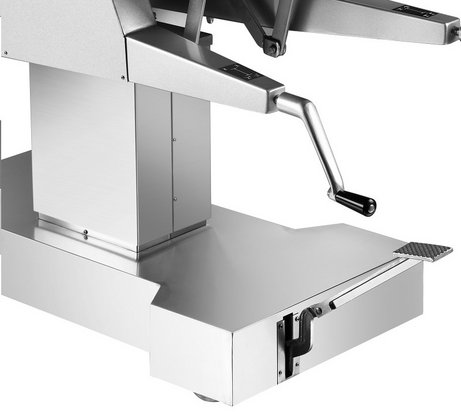
Hermetic laser welding for medical devices
Hermetic sealing electronics in medical devices, such as pacemakers and other electronic products has made fiber laser welding the process of choice for applications requiring the highest reliability. A recent advance in the hermetic welding process has addressed concerns about laser welding and the end point of the weld, a critical location point in completing the hermetic seal. Previous laser welding techniques resulted in a depression at the end point when the laser beam is turned off, even when ramping down the laser power. Advanced control of the laser beam like our wobble technology eliminates the depression in thin and deep-penetration welds. The result is consistent geometry and lack of porosity at the end point with improved cosmetic appearance and more reliable hermeticity.
Precision machined laser welding
Seals used in pharmaceutical manufacturing were originally TIG welded. Because of their use in sensitive environments, these components are precision machined and ground from high-temperature and chemical-resistant nickel-based alloy material. Lot sizes are usually small and the number of setups is many.
The assembly of these components has been improved using fiber laser welding. Justification to replace the earlier robotic arc welding process with fiber laser welding using a four-axis cartesian coordinate machine tool includes consistently higher quality of the laser welds, ease of changeover from one component configuration to another reducing setup time, and improved throughput and decreased assembly costs by automating the laser welding process using a four-axis CNC laser machine.