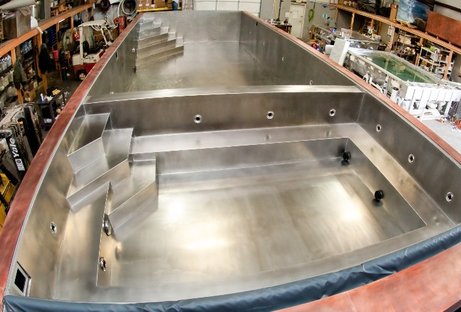
Why Use Stainless Steel in Pool Areas?
Stainless steel is a popular choice for pool areas because of its long life, low maintenance costs, design flexibility, and hygienic benefits. Its ease of bacteria, virus, and algae removal is comparable to glass, making it the hygienic choice for pool applications, therapy facilities, and other applications where cleanability is critical.
Seismic performance is an additional important benefit. Stainless steel swimming pool liners have withstood earthquake damage under conditions where traditional concrete and fiber-reinforced polymer (FRP) pool linings have failed.

Design Advantages
While most people are familiar with the classic applications for stainless steel, many popular new design concepts are naturally suited to this flexible material. These include integral fountains, infinity edges, and other creative elements. Vacation venues and theme parks use stainless steel liners for water rides, elaborate pools, and even endlessly flowing rivers with currents that carry bathers along their curving paths.
Stainless steel’s design flexibility makes possible creative designs like this Type 316 continuously flowing beachside river.
Stainless steel pool liner and structural support systems are designed in advance and can be installed more rapidly than traditional systems. This is advantageous when relining commercial and public pools, and for new construction projects when it is desirable to limit construction disruption and pool closure time.
Spa & Therapy Pools
Therapy pools were one of the early applications for stainless steel liners because of their hygienic requirements, but stainless has also become popular for the growing number of spa and hot tub pools found in private residences, resorts, and public facilities.
The higher temperatures used in these pools can increase bacteria and virus levels. Higher chlorination levels are typically used to disinfect them, making these application environments more corrosive than that of the typical recreational pool. Stainless steels are a logical choice, but Type 316 or a more corrosion resistant molybdenum-containing grade should be selected.