Laser Welding in Sheet Metal Fabrication
Many sheet metal fabrication shops still hesitate to invest in laser welding.
They are missing out on the numerous competitive advantages and opportunities that it offers over conventional welding processes.
As one of the most substantial advancements in modern welding technology, the laser welding process allows industry professionals to achieve much higher precision and speed in welding operations.
Additionally, products manufactured using the process perform at least as well as those produced using MIG or TIG—if not better—with lower overall production costs and shorter lead-times.
Here are some insights that you need to know:
HAZ (Heat affected Zone) is reduced to almost non exisiting compared to Arc Welding
Due to the small spot size of the laser, the heat input is typically 200 times lower than with arc welding processes like MIG, MAG or TIG welding.
Laser welding has been widely accepted by the automotive industry for decades, but in sheet metal fabrication many shops are still hesitant to take the leap. The latest advancements have made laser welding a more viable solution, reducing the cost of entry and providing sheet metal fabricators greater access to the numerous advantages laser welding offers compared to conventional welding processes.
In heat conduction welding, cosmetic weld seams with smooth surfaces result and often eliminate or dramatically reduce secondary processes like grinding or straightening. Typical applications include covers and boxes, or fixtures such as countertops and sinks for the medical or food service industries.
With deep penetration welding, weld speeds of 1000 mm/min to 5000 mm/min, in combination with high weld strength, can be realized. This welding technique is used when full penetration, high part stiffness or sealed and tight weld seams are required. Applications include pressure tanks, brackets or flanges.
Both techniques offer consistent weld seam quality, decreased heat input and negligible distortion of welded components.
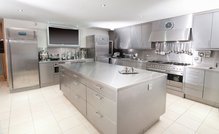
Cost Reduction in sheet metal fabrication by laser welding
Manufacturers benefit from any process that reduces cost per part—and laser welding has many advantages in this regard. Due to the low heat input of this process, distortion and discoloration can be avoided to completely eliminate the need for refinishing. As these postprocesses are extremely time consuming and expensive, the costs per part are significantly reduced. Furthermore, laser welding speeds are considerably higher than conventional processes, which often greatly reduces processing times. This leads to free capacity on the machine, allowing the manufacturer to serve more customers.
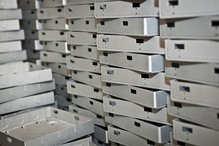
Increased functionality in sheet metal fabrication by laser welding
Laser welding is not only about reducing costs, but also increasing functionality. A smooth surface with an extremely narrow welding geometry is beneficial for kitchen, furniture and other industries where visible weld seams are common. Due to the low heat input, manufacturers can avoid discoloration and achieve highly aesthetic parts directly from the machine. One can also achieve very strong seams for parts that require strength. The characteristic seam geometry of laser welding leads to full penetration of the parts while reducing the influence on the grain structure. Tensile strength tests show conventionally welded seams break in the welding seam, while laser welded parts break in the base material.
Laser welding also offers unique seam geometries enabling the part designer to reduce weight, material and costs, such as replacing spot welds with overlap joints that are not only stronger, but also invisible from the other side. Laser welding is the next logical step and Lasermach has the know-how to support the implementation of this technology in your production process.
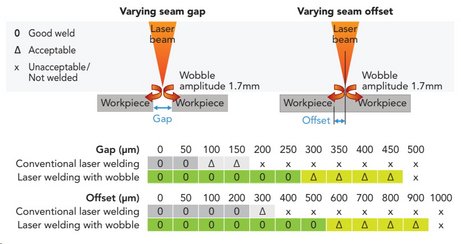
Due to the small spot size of the laser, the heat input is typically 200 times lower than with arc welding processes like MIG, MAG or TIG welding.
To fully reap the benefits of laser welding, a fabricator must commit with a normal laser welding machine to high-quality sheet metal processing prior to welding.
As a rule of thumb: material gaps in the weld zone should be limited to approximately maximum 0.10~0.12mm, although this can limit can be extended to gaps of 0.50~0.80mm and more with our new wobble3+ laser welding torch with adjustable welding width.
Luckily, these tolerances are easily met by modern 2D laser cutting machines and press brakes. Although parts can typically be converted from arc welding to laser welding with just minor adjustments to the design, laser welding does provide design engineers with new opportunities, such as overlap welds, corner welds and flange welds. Even complex joint geometries like curved shapes or materials with different sheet thicknesses can be laser welded easily.