Laser Brazing
Brazing is a joining method for joining two or more metal parts together. The primary difference between welding and brazing is that welding involves the melting of the base material, whereas brazing involves melting only a filler metal which is flowed into the joint to create a bond between the base parts. A principle consideration is that brazing occurs at a lower temperature than welding, through the practice of selecting filler metals that have a lower melting temperature than the parts to which it will bond.
- Non-similar metals can be joined together
- Lower temperature brazing has less potential for distortion
- Can eliminate the need for trim moldings
- Reduced materials and manufacturing steps reduces costs
- Simplification of painting and color-matching process
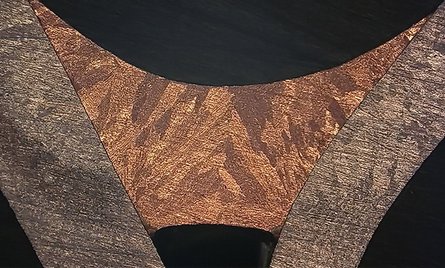
Manufacturers Discover the Benefits of Laser Brazing
The list of benefits that come along with the use of laser brazing keeps growing. Not only does laser brazing accomplish feats that traditional joining techniques can’t, but it also offers increased flexibility and speed, alongside reduced materials and manufacturing steps which in turn reduces cost.
Brazing is a method that is extremely effective at joining two or more metal parts together. It differs from welding in that instead of melting a base material, a filler material is melted and flowed into the joint to create a bond. Since brazing uses filler material, the process allows for the joining of non-similar metals.
Also, since brazing takes place at much lower temperatures than welding does, there’s a lower risk for distortion of the base metal components. Lastly, the reduced number of materials needed for the brazing process reduces costs along with less required manufacturing steps.
Traditional brazing techniques include torch brazing, arc brazing, furnace brazing, and induction brazing. Torch brazing involves the use of a gas flame held near the joint to heat the filler material. Arc brazing uses an electrical current to heat the filler. Furnace brazing requires the heating of the entire assembly. And induction brazing uses induction heating to melt the filler material to join parts.
Laser Brazing Takes the Next Step for Brazing Technology
Fiber laser brazing technology adds a level of precision where conventional brazing methods fall short. The laser quickly melts the filler material with even less heat distributed to the base metal parts. Laser brazing also doesn’t require any flux, further reducing material costs. With the elimination of heat to the joined parts, throughput is increased.
The fiber lasers used for laser brazing are often entirely solid-state designs and require minimal maintenance. This makes laser brazing ideal for industrial environments where uptime is critical. Hot-swap redundancy solutions are available to eliminate downtime and keep the laser beam operational under all conditions.
Laser brazing goes perfectly with automation solutions. Both the firing of the laser and its path can be controlled with robotics and software. Manufacturers are able to eliminate the variability that manual operators bring to the process. Every laser brazed joint is identical to the last thanks to the laser’s high beam profile and power stability.
Benefits of laser Brazing Over Welding
Brazing is a method that is extremely effective at joining two or more metal parts together. It differs from welding in that instead of melting a base material, a filler material is melted and flowed into the joint to create a bond. Since brazing uses filler material, the process allows for the joining of non-similar metals.
Also, since brazing takes place at much lower temperatures than welding does, there’s a lower risk for distortion of the base metal components. Lastly, the reduced number of materials needed for the brazing process reduces costs along with less required manufacturing steps.
Traditional brazing techniques include torch brazing, arc brazing, furnace brazing, and induction brazing. Torch brazing involves the use of a gas flame held near the joint to heat the filler material. Arc brazing uses an electrical current to heat the filler. Furnace brazing requires the heating of the entire assembly. And induction brazing uses induction heating to melt the filler material to join parts.
Fiber laser brazing technology adds a level of precision where conventional brazing methods fall short. The laser quickly melts the filler material with even less heat distributed to the base metal parts. Laser brazing also doesn’t require any flux, further reducing material costs. With the elimination of heat to the joined parts, throughput is increased.